The Best Guide To Alcast Company
The Best Guide To Alcast Company
Blog Article
Getting My Alcast Company To Work
Table of ContentsSome Known Factual Statements About Alcast Company The 9-Second Trick For Alcast CompanyThe Alcast Company PDFsNot known Incorrect Statements About Alcast Company Some Known Details About Alcast Company The Basic Principles Of Alcast Company The Single Strategy To Use For Alcast CompanyThe Single Strategy To Use For Alcast Company
It possessed good stamina and machinability. There are several other light weight aluminum alloys that can be utilized for casting components. To locate out which alloys would certainly benefit your jobs, get in touch with Impro.
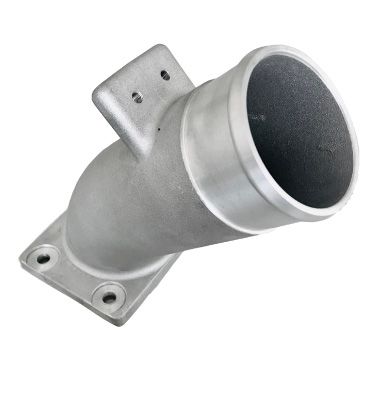
(AA), based in North America, has actually produced specifications that control aluminum alloys' structure, residential properties, and nomenclature. There are 2 types of light weight aluminum alloys functioned and cast.
Alcast Company Fundamentals Explained
Cast light weight aluminum alloys are made by melting pure aluminum and incorporating it with various other steels while in liquid type. The mix is put into a sand, pass away, or investment mold and mildew. After solidification, the metal is eliminated from its mold. At this phase, it remains in either its last kind or as a billet or ingot for further processing.
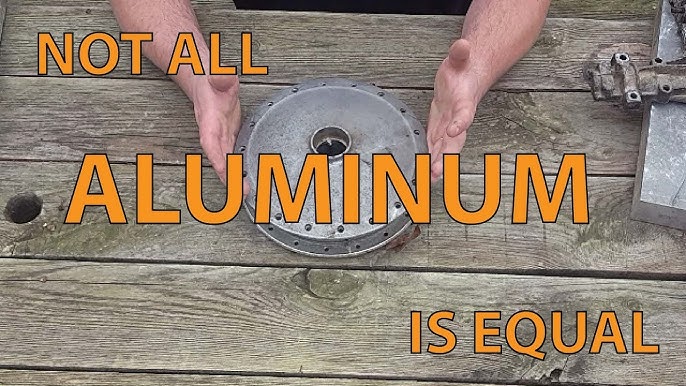
There are many minor distinctions in between wrought and cast aluminum alloys, such as that cast alloys can contain extra significant quantities of various other steels than wrought alloys. The most remarkable distinction in between these alloys is the manufacture procedure via which they will go to supply the final item. In addition to some surface area treatments, cast alloys will certainly exit their mold and mildew in practically the exact solid kind desired, whereas functioned alloys will certainly undertake several adjustments while in their solid state
The Ultimate Guide To Alcast Company
If you believe that a functioned alloy might be the best for your task, take a look at several of our posts that explain even more about particular functioned alloys, such as Alloy 6061 and Alloy 6063. On the various other hand, if you assume an actors alloy would be much better for you, you can discover more concerning some cast alloys in our Alloy 380 and Alloy 383 articles (coming quickly).
When selecting an aluminum factory for your manufacturing needs, it's critical to study several aspects. One of one of the most important elements to consider is the experience and capability of the factory. Selecting a shop that has the appropriate knowledge of the light weight aluminum spreading process, and the profile to show for it, aids to have a successful outcome for your job.
What Does Alcast Company Mean?
Having the experience and market knowledge to engineer your spreadings for ideal manufacturing and top quality results will improve the project. Making aluminum spreading needs a complicated set of processes to achieve the best results. When picking a new aluminum foundry to companion with, ensure they have considerable industry experience and are educated about all elements of the aluminum spreading procedure: design, manufacturing, material analysis, and item testing.
The foundry ought to additionally have a proven track document of supplying extraordinary items that satisfy or exceed customer expectations. Quality assurance should additionally be at the top of your checklist when choosing an aluminum shop. By dealing with a qualified shop that complies with the requirements for quality assurance, you can secure the honesty of your product and guarantee it satisfies your specs.
The 8-Second Trick For Alcast Company
By choosing a firm that supplies solutions that meet or surpass your item demands, you can be certain that your task will be completed with the utmost precision and efficiency. Different parts require different production strategies to cast aluminum, such as sand casting or die casting.
Pass away spreading is the name provided to the process of producing complicated metal elements with use molds of the component, likewise known as passes away. The process uses non-ferrous metals which do not include iron, such as light weight aluminum, zinc and magnesium, as a result of the desirable buildings of the metals such as reduced weight, higher conductivity, non-magnetic conductivity and resistance to corrosion.
Pass away spreading production is quick, making high production levels of elements easy. It generates more parts than any kind of other process, with a high level of precision and repeatability. To read more about die casting and die casting materials made use of at the same time, read on. check There are 3 sub-processes that fall under the category of die spreading: gravity die casting (or permanent mold and mildew casting), low-pressure die casting and high-pressure die spreading.
Alcast Company - The Facts
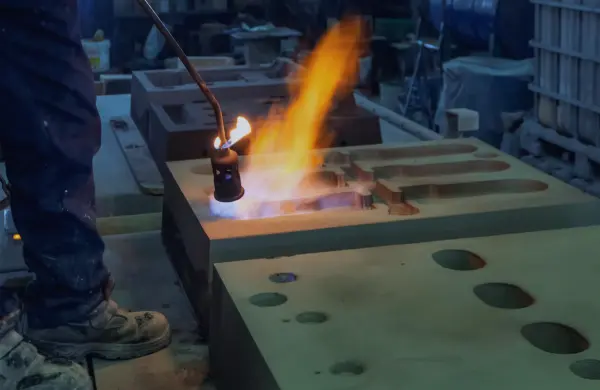
The pure metal, additionally referred to as ingot, is contributed to the heater and kept at the molten temperature of the steel, which is then moved to the shot chamber and injected right into the die. The stress is then maintained as the steel strengthens. Once the metal solidifies, the cooling procedure starts.
The thicker the wall surface of the component, the longer the cooling time due to the quantity of indoor metal that likewise needs to cool. After the component is fully cooled, the die halves open and an ejection device presses the part out. Complying with the ejection, the die is shut for the next shot cycle.
See This Report about Alcast Company
The flash is the extra product that is cast during the process. Deburring gets rid of the smaller sized pieces, called burrs, after the cutting process.
Nevertheless, this proved to be an incorrect test, due to the fact that the tester might cut into a piece and miss out on a location with porosity. Today, top suppliers use x-ray testing to see the entire interior of elements without cutting right into them. This permits them to much more properly approve or reject parts. To reach the completed product, there are 3 primary alloys used as die spreading material to select from: zinc, light weight aluminum and magnesium.
Zinc is one of the most used alloys for die casting due to its reduced expense of raw products. Its rust resistance additionally allows the elements to be long enduring, and it is one of the much more castable alloys due to its reduced melting point.
Indicators on Alcast Company You Should Know
As pointed out, this alloy is one of one of the most typically utilized, yet makes will, at times, select light weight aluminum over zinc because of aluminum's manufacturing benefits. Aluminum is very affordable and one of the more functional alloys. Aluminum is used for a number of various products and industries anything from home window frames to aerospace materials.
Report this page